Examples of polymer uses: Joint materials Waterstops Membranes Bearing pads Conduits, pipe...
25 Incredible Concrete Repair Tips for Pros using Epoxy
- Surface prep is vital
As in many other construction activities, taking proper steps to properly clean and prepare surfaces prior to the use of repair materials is critical to the time efficiency and long-term success of your repair. Surface preparation methods include (from gentle to aggressive) detergent scrubbing, acid etching, grinding, abrasive blasting, steel shotblasting, scarifying, needle scaling, high pressure water blast, scabbling, flame blasting, bush hammering and milling/ rotomilling.
Note that some abrasive methods may leave a thin film of dust on the surface which should be flushed with a high-pressure water blast. For protective coatings, often a shotblast is the best first step with the goals of removing all contaminants, opening pores and light cracks and providing a roughened surface profile resembling 40 grit sand paper (such as ICRI CSP 3). For spalls and crack repair, it is essential to remove all concrete laitance, surface contaminants and traces of form or release oils and curing compounds using some form of abrasive removal.
If you are considering pressure washing, 5000 psi has been determined as the minimum pressure to provide acceptable levels of cleaning of concrete surfaces. In cases where the cementitious surface was overworked when placed or excess water was used, it is highly recommended that the paste layer be partially or completely removed for the optimum performance of the repair. Applicable specifications include: ACI 503R, ASTM 4263, ASTM 4260, ICRI 03732 and ICRI 310.2.
2. Elcometer tab pulls
Even with the best surface preparation (and a small mock-up), unexpected issues can interfere with good surface bonding. For a small investment, you can test the bond of any repair material or coating in suspect areas relatively quickly using small circular metal tabs. The whole process is explained in ASTM D4541, a test handled by an Elcometer 106 portable pull tester. Consider that this test has been known to have reproducibility issues, so use plenty of dollies in your evaluation. You can also make a home-built version that uses 2” diameter pipe caps (ground flat) and an Enerpac® hydraulic cylinder (if you elect this option, have a third party check the calibration).
- Provide a mockup when feasible
This preconstruction step demonstrates that you are willing to take the extra care to ensure a quality project. This tactic is especially useful if you are planning to use a new material. Disagreements should be minimal when the actual appearance is presented before the project starts. Sometimes, you can be compensated for your time and materials.
- Save $ with local aggregates
For polymer repair mortar or grouts, many (if not most) manufacturers package their aggregate filled systems in a 3-package system which includes bags or pails of graded sands.
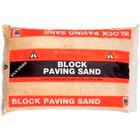
Unfortunately, shipping a low cost and dense product such as sand around the country or overseas is very costly and we don’t think that it is necessary. Call us when you develop a requirement for this type of a system and we’ll provide recommendations to locally source a gap graded aggregate system that can provide significant savings for you and your customer. Use only dried sand (less than 0.2% moisture) in polymer mixes.
- Estimate with a waste factor margin
For most of the repair jobs (not counting coatings) where epoxies and other polymeric products are used, the material cost is typically within a range of 5-10% of the total job costs which include other materials, equipment, mobilization and labor. If you estimate conservatively and your guys run short, there may be several negative consequences.
First, the guys might shortcut the application rate which might undermine the performance of the areas that were short. Second, they might run out and call you on late Friday afternoon looking for a very costly delivery by air on Saturday, or your crew might have to re-mobilize because the owner needs the area back in service while awaiting the replacement material. There isn’t much cost risk in buying a little extra as epoxies are very long-lived materials so you can use them on future projects or return them in unused condition (we charge a 15% return fee).
If you elect to buy a little extra material, you likely just saved a lot more on your most expensive cost item which is labor. Finally, if your guys discover a bit of extra work not originally noticed, you have an option for a change order without excessive costs.
- Operate safely
Maintain copies of all SDS (safety data sheets) to be easily accessible on site. Don’t assume that because you’ve worked in the industry for 30 years that the content of the SDS is the same as in 1982—they are frequently updated and the contents are subject to change. For example, in the case of accidental ingestion of a toxic substance, syrup of ipecac is no longer routinely suggested.
Make sure that your guys wear the proper PPE even in hot/humid weather. The minimum level of protection for handling chemical polymers for concrete repair typically includes long sleeves, long pants, rubber gloves and safety glasses (with side shields). Other levels of PPE can include face shields, goggles, Tyvex® or other synthetic outer clothing, dust and organic vapor masks and hearing protection. PPE training should ensure the technician knows how to remove protective materials without contaminating himself so a trip to the washroom or food trailer doesn’t mean more exposure. On many jobs, a good hygiene habit is to wash hands before and after restroom breaks.
In some individuals, certain chemicals can cause an allergic sensitivity that can be triggered over repeated exposures and make working in the field impossible. Encourage your employees to clean their work clothing regularly rather than allowing contaminants to build up. Finally, don’t assume your guys will think about drinking sufficient water on the hottest days—you will have to keep reminding them.
- Soap and water vs. solvents
For cleaning epoxies and other polymers from tools, many field techs use acetone or MEK. If there are only minor amounts of product to be cleaned and the bulk material is uncured, you can squirt a bead of liquid dish-washing soap right on the tool surface and rinse off the blade or surface with hot running water. Many of the polymers will emulsify and rinse off if you use a little extra concentrated soap which is far less costly (and never flammable) than solvents. The same technique works on cleaning exposed skin—liquid detergent is better for your skin than acetone. Some contractors swear by using film forming liquid skin protectant creams for the times when the gloves are off or as a great secondary barrier practice.
- Save cardboard
Instead of disposing of large cardboard shipping cartons, have your warehouse guy save them and cut them into 12”x 12” (or some other favorite size) squares to use as mixing platforms for small quantities of 2 component polymers or for making small paste mixes. When the project is over, you can toss the cardboard as the epoxy scraps should be in the hardened form of a cured inert plastic.
- Always take pictures
Your project site pictures have a value far in excess of 1000 words. An absolute job requirement is that your foreman takes shots before and after every job. These are helpful in many ways: establish baseline conditions, provide visual backing for change order situations, be used in safety training, assist in accident investigations, provide evidence of quality work and project completion, are valuable for marketing, establishing credibility and to help educate new employees.
- Timing an industrial floor or concrete deck epoxy coating
Plan your projects so the preparatory steps take place in the morning. Avoid placing impermeable coatings (includes most high solids epoxies and polyurethanes) during periods of rapidly rising temperatures which is usually morning to early afternoon (especially in situations without climate-controlled environments). In most areas, the daily temperature cycle has reached its maximum around 3-4 pm (15-1600 hours) so this is a great time to start the coating. This late day timing minimizes the potential for high rates of vapor transmission to interfere with the success of the coating. If the building has a functional heating/cooling system, the air conditioner should be run for at least 2 days prior to the coating to minimize the same issues.
- Don’t wait 30 days for 'full' concrete cure
We offer several primer solutions for bonding, repairing or coating green concrete including QuikPrime which even works underwater. You can generally use CCS Coating, QuikPrime 24 hours after concrete placement.
- Hammer your concrete
Don’t attempt to fix delaminated concrete without confirming and mapping the extent of the problem. Bring a sounding hammer and test the area to be repaired. A heavy steel chain can also be used. Cracks and spalls will sometimes be caused by poorly bonded topping slabs or old repairs which have disbonded or never bonded over the original damaged substrate. Concrete can debond from the steel deck in elevated slab on pan installations. If the concrete is delaminated in areas, fixing the cracks without repairing the underlying delamination is a waste of time. Be prepared to consider the cause(s) and offer a fix for the delamination as first steps in the repair.
- Heat is speedier (epoxy thermodynamic tip)
Most ambient temperature cure epoxies exhibit reaction rates that increase or decrease by a factor of 2 for every interval of 18°F (10°C) change in temperature. If your epoxy repair material is curing too slowly, gently add heat to speed cure times.
There are many techniques for heating which include: heat guns, warming blankets, pre-heating the cans of epoxy before use, warming the substrate with local baseboard heaters contained with temporary walls of plastic sheeting, etc. It’s best to use temperatures below 300°F (150°C) for speed curing (this includes heat guns). Since epoxies react by giving off heat (in an exothermic reaction), the thicker you apply an epoxy, generally, the faster it cures. Conversely, if your summer temperatures are very hot, the amount of useful life of epoxy mixes may be too short for practical use. In this case, cooling the separate components before use in an ice bath or air-conditioned area will help extend the mixed life.
- Get thinner with heat
If your epoxy is too thick, preheat the components before mixing. Store the epoxy containers overnight in a closet with a portable heater or put them in the cab of the truck with the heater turned up when it’s cold outside. Some field technicians mount a light bulb inside their epoxy injection pump to warm the epoxy in the reservoirs. An epoxy with a viscosity of 1000 cPs at 50°F might have a viscosity of only 150 cPs at 80°F. Don’t forget that useful (mixed) lives and cure times are also affected by temperature.
- Polymers shrink
Epoxies and other polymers have a curing property that is rarely discussed. When A + B components are mixed in proper proportions, most polymers exhibit both linear and volume shrinkage upon cure. This is because the newly formed cross-linked polymer takes up less space than the separate unreacted components. Shrinkage is factor that must be considered when the use of repair polymers might involve a thick cross-section of cured material.
How thick is too thick before you will develop a problem such as internal stresses in the repair? The answer is that it depends on the specifics. There are some tactics which include the use of installing multiple lifts, low exotherm and/or low modulus resins and aggregate filled epoxy systems which help alleviate problems when thicker cross-sections of repair materials are needed. Please call us for advice.
16. Polymers move more
In addition to shrinkage upon cure, remember that most concrete repair polymers including epoxies have a thermal coefficient of expansion that is greater than that of other substrates such as concrete or steel. How much different varies with the polymer and whether it is filled with inorganic solids. A generalization is that the polymers expand or contract with heat or cold temperature changes about 5-10 times more than concrete or steel over the same temperature change. This is another critical factor to consider when placing large (thick) cross-sections of polymer repair materials. Call us for specific advice.
- Moisture vapor can drive you crazy
Standard practice for concrete floor construction today is to install a vapor barrier between the structural slab and underlying compacted earth or engineered fill. This practice is relatively new, so what can be done with older concrete floors which don’t have a vapor barrier? Today, if your moisture test shows 3 lbs/1000 sq. ft/24 hrs or more of moisture vapor transmission (ASTM F18690), don’t even think about installing an impermeable coating or flooring material without first using an epoxy vapor barrier.
We make a great product for this purpose called MVR Coating. When properly used, it will reduce the vapor drive to a safe level and can be topcoated in about 12 hours.
- Width matters
Before embarking on an epoxy crack injection repair, get a good idea of the average width and depth of the cracks. How? You can start with using a plastic crack card and graduate to a lighted portable crack scope. Remember that for smaller projects, you will consume more epoxy by flushing the gun and cleaning that probably will be used in the cracks. So on smaller projects, your waste factor can be over 50%. Don’t be caught short on materials.
- Roll your ports
Surface ports have become a popular tool to use with epoxy injection. Yet, they can also lead to poor performance on these projects if they are plugged or fall off in use. When placing ports with a paste adhesive, it is critical that the adhesive doesn’t plug the barrel of the port over the crack. Some contractors have found that mixing their paste adhesive on a piece of cardboard and then rolling the flange of the port through the adhesive (rather than using a trowel to apply paste directly to the base) works best. Others insert a cocktail straw or toothpick into the port to hold it in place and ensure continuity into the crack.
- Epoxies last longer
When your project is complete, don’t automatically react off your leftover A and B components to dispose of partial containers of epoxy. Most epoxy products are relatively stable and can be used for extended periods if kept within a reasonable temperature range and sealed. We say that most of our epoxy products can be safely used within 3 years of manufacture. There may be some settling (particularly for coatings) but the products will still perform if the separate components are mixed well individually before use. Caution: moisture sensitive materials such as polyureas or polyurethanes may have a much shorter shelf life.
- Cosmetic surgery for concrete
Say you have a sound substrate with a myriad of different tones or slight cracks or chips that disturb the smooth face. What can be done? Consider sacking, a repair technique that involves pre-wetting the substrate and then hitting the surface a burlap sack containing fine aggregate of the same color as the concrete along with some Portland cement. A fine wet cement-based slurry can also be applied by heavy brush. This trick can also rid the substrate of the dark crack “shadow” following epoxy crack injection on architecturally sensitive surfaces such as light precast panels—call us for more information.
- Bulk loaders work for epoxy too
Contractors who specialize in caulking and waterproofing may use bulk loaders to shoot single component elastomeric caulks. For delivering both liquid and paste viscosity epoxies, bulk loaders come in a wide variety of gun types and applicator tips including battery and pneumatic operated. They can be used with two-component epoxies as long as the mixed material has an extended potlife. The biggest reasons to consider a bulk loader are time and material savings—they can easily be loaded from a bulk mix in a 5-gallon bucket, placed just where needed and epoxy products sold in bulk are less costly. For larger projects, air-driven two-way bulk loaders might offer additional efficiency. Albion Engineering is a great place to look for a wide selection.
- Use a scale
On all of our data sheets, we include the separate weights of parts A and B. Why? We have noticed many other manufacturers require that all of the materials in multiple containers be used to make a mix. Yet, we know that not every project needs all of the materials in our containers and we hate wasting good materials. Of course, you can also judge proper quantities by filling clear plastic measuring cups or pails, but the safest way to reproducibly get accuracy is to pre-weigh both components since the weight is not affected if the container becomes too dirty or colored to read the volumes on the sides. Just remember that a material which is 2:1 by volume is not likely to have the same ratio by weight.
- Join up
ACI and ICRI are international members-driven organizations where you can meet in local chapters or attend regional and national conventions twice a year to learn more about concrete and its repair. Many of the attendee members have been performing the same specialized concrete repair specialties and are happy to share success stories.
- Come to our class
We organize free training sessions in structural concrete repair and epoxy injection two or three times a year—they take a day and a half. It includes hands-on practice and technical lectures. Call (650.261.3790) or email us if you’re interested.