Concrete cracks. It's a fact of life. Some cracks might not need attention while others could have...
Stitching for Structural Concrete Repair
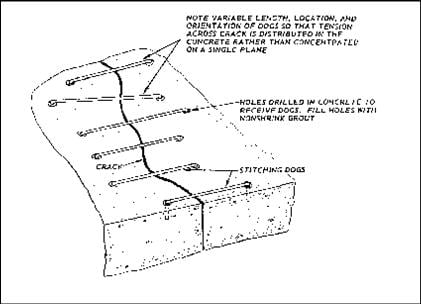
Is there a simpler, low cost method to provide additional support to existing structures?
Yes, the non-proprietary procedure is a related to steel plate bonding and it is commonly called rebar stitching. It may often be an efficient alternative to glass or carbon fabric wrapping, but since no company is actively marketing it, often the structural engineer or architect doesn’t even consider this repair option. The repair is often fast, inexpensive and requires no special tools. This procedure stands the test of time: the pictorial diagram above is from an old U.S. Army Corp of Engineers concrete restoration design from the early 1960's, while the picture below is a recent project on a suspended slab.
Installation is straightforward. First, it is critical to know the depth of coverage (and possibly the location) of the existing reinforcing steel so that the old (internal steel) reinforcement is not damaged during the installation of stitches (some concrete is unreinforced so this concern may not exist). The location of structural steel is listed on the original design drawings. The architect or engineer calculates a requirement for increased strength, estimates a safety factor and then develops a pattern of steel or FRP reinforcing bar to be installed.
The contractor saw cuts channels at specified depths (generally less than 2" deep) in the concrete surface, ties the bar together at intersections, then fills the channel with a structural liquid epoxy or paste epoxy adhesive. If the channel lies on a horizontal deck, the filling is by gravity, otherwise the channel may need to be sealed with a temporary overlying form so the epoxy paste or liquid can be pumped into the hollow space. Unlike fiber wrapping systems, dowel holes can be drilled in any direction to better anchor the bar placed in the surface channels and the bar can cross the joint or crack at any angle.
For deeper slabs and in instances where there is no existing reinforcement, it may be a preferable strategy to drill at a 35-40 degree angle from each side of the crack, inserting the bar at an angle fully into the deep hole rather than cut a groove. ChemCo Systems CCS Bonder Liquid LWL and CCS Bonder Paste LWL are two structural epoxy adhesives frequently used for this application. Both adhesives pass the ASTM C881, Type IV specification for structural load bearing applications.
What type of concrete repair might qualify as a candidate for rebar stitching? Parking and bridge decks, slab on pan floors, locally overloaded areas, missing or insufficient rebar, slab and vertical foundations, anchoring large patches and spall repairs to sound concrete, beams and piers all might be excellent stitching applications. Stitching benefits include: a) fast installation, b) localized repairs, c) low material and labor costs, d) no special equipment required, e) damp and wet substrates are OK (see adhesive requirements) and f) repaired surface can bear traffic.
Call or write us if you need an adhesive recommendation or more practical tips for stitching.